Printer Distributor Gets Cusom Packaging Solution
Last updated on
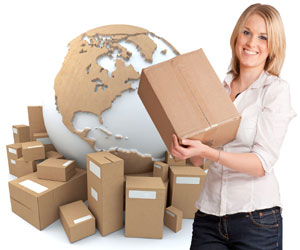
Korrvu® Retention Packaging and NewAir I.B.® 200 System Provide Printer Distributor with Custom-Packaging Solution
Located in Rhinelander, Wis., Laser Pros International (LPI) is one of the world’s largest distributors of laser printer parts and accessories. The company has grown tremendously since its origin in 1990 when it began out of president Steve Spencer’s home. LPI currently employs more than 100 people and its corporate headquarters occupies 40,000 square feet.
LPI’s concern for protecting the environment while reducing material and shipping costs has always been important.
Mike Egan, warehouse manager for LPI, began looking for a more economical packaging alternative for the shipment of its products in 2007. The rising cost and supply issues of its existing fabricated foam packaging became a real concern for LPI. In addition, the company was looking for a package that would be easier to recycle.
Above all, the delicate nature of the products required safe, dependable packaging. Laser printer parts contain fragile pieces that, if broken, can render an assembly worthless. LPI needed a new packaging solution that decreased the dimensions of the package and used recyclable protective materials without compromising protection or increasing material costs.
“We distribute domestically and internationally to a wide range of customers– from small service providers to some of the largest in the world,” said Egan. “Many of our customers require next-day delivery, so there is a real emphasis on damage-free products arriving in a timely manner.”
‘SHIFT’ing Methods
Sealed Air’s cushioning sales representative Mark Nennig and Korrvu® specialist Doug Graf introduced Egan to a perfect packaging solution to meet those needs – a hybrid pack which used Korrvu® retention packaging and NewAir I.B.® inflatable cushions on the top and bottom for additional protection.
Korrvu® retention packaging uses a proprietary retention frame and elastomeric film to hold the items securely in place during shipment. The resilient film membrane conforms to the shape of the product being packed, providing a versatile, custom-designed packaging solution. In addition, since the retention frame uses corrugated material for structure, the packaging stores flat to reduce storage requirements and recycles in the corrugated recycling stream.
The NewAir I.B.® 200 inflatable packaging system is a fast, flexible and all-electric inflatable cushioning solution designed to increase productivity and free up valuable warehouse space. The packaging system automatically inflates and dispenses ¾-inch height patented Barrier Bubble® cushioning material.
LPI’s new packaging process is simple. The corrugated boxes are assembled and a sheet of NewAir I.B.® cushioning material is placed in the bottom of the box. The product is loaded into the Korrvu® retention frame by folding up the side flaps to loosen the film and form an insertion pocket, sliding the product between the resilient film and corrugated base, and folding the flaps down to tighten the film and hold the product securely in place. The insert is loaded into the shipping carton and a final sheet of NewAir I.B.® cushioning is added to protect the smaller, more fragile parts of the product.
“The new Korrvu® method is less complicated than our old method and more aesthetically appealing,” said Egan. “In addition, the Korrvu® retention film serves as an extra layer of surface protection.”
The new process has substantially simplified the steps and reduced the resources necessary for LPI’s packaging process. Prior to switching to the new Sealed Air packaging solution, LPI needed to use various combinations of cut polyurethane foam, cut polystyrene and polystyrene peanuts to protect its products during shipment.
The old process required more time, more material and more costs.
“Our old packaging method required three packagers to keep up with the packaging line and resulted in a bulky box with a high dimensional weight-based shipping cost,” said Egan. “We ultimately decided to test the protection provided by the Korrvu® packaging because we knew it was recyclable and would decrease our package dimensions, which translates to customer savings in shipping costs.”
‘ENTER’ing Testing Phase
Working closely with LPI at Sealed Air’s Package Design and Development Center in Chula Vista, Calif., packaging engineers developed a custom package design that met all of LPI’s specific needs.
“In addition to performing ISTA 1A testing, we tested the packaging by shipping the products back and forth between the LPI headquarters in Wisconsin and the Sealed Air Package Design and Development Center in California,” said Egan.
The new solution passed all the tests and Mike Egan was convinced to make the switch. The entire process from introduction to full implementation took less than six months.
‘TAB’ulating Results
As a result of successfully implementing the Korrvu® packaging process, LPI’s packages now have smaller dimensions and require less material – making the packaging more environmentally responsible and cost-effective for the company and for its customers.
Because Sealed Air’s new packaging solution reduced the dimensional weight of each package by almost half, Egan estimates 25 percent savings on shipping costs.
“Whenever we approach any packaging project, we want to make sure it offers an enhanced customer experience, improved efficiencies and reduced costs to our product,” said Egan. “In this case, we did all three. In addition, the package provides superior presentation. We couldn’t be more pleased with the result.”
As an added bonus, Korrvu® retention frames store flat, resulting in a two-thirds reduction in storage space savings for LPI. Egan said “LPI likes the new design and appreciates the fact that it’s 100 percent recyclable.”
‘ALT’ernate Solutions
In addition to the NewAir I.B.® 200 system and Korrvu® retention packaging, Sealed Air provides LPI with a Fill-Air® NTS inflatable packaging system, which quickly converts compact rolls of specially formulated tubular material into continuous, perforated chains of air-filled material for professional-looking void fill.
“Our customers disliked the polystyrene peanuts because they clogged mechanical parts of the assemblies and created a mess at their facility,” said Egan. “We were able to replace the majority of the polystyrene peanuts we used with Fill-Air® cushions for void fill.”
LPI also uses an Instapak® 901 handheld foam-in-place system and Bubble Wrap® brand cushioning for its larger products. While Bubble Wrap® brand cushioning provides surface protection during shipment, Instapak® foam packaging provides protection against shock and vibration.
‘FUNC’tional Future
“Sealed Air partnered well with us and knows what we’re looking for,” said Egan. “Their recommendations are invaluable. As new products are developed, Mark and Doug bring them to our attention.”
Sealed Air and LPI continue to explore ways to work together on packaging solutions that protect the products that LPI’s customers need and help the company remain environmentally responsible.
About Laser Pros International
Steve Spencer, president, formed Laser Pros International (LPI) in 1990. Specializing in HP LaserJet printers, LPI provides the industry with the highest quality products and services at competitive prices. Our warehouse has $5M in inventory and stocks a complete range of products, components, supplies, accessories, documentation, and whole printers. While marketing the highest quality products and services at competitive prices, the company’s focus is to add value to Hewlett Packard, Lexmark and Canon printer service and repair companies. Laser Pros International is located in Rhinelander, Wis. For more information, visit
www.laserpros.com or call 888-558-5277.
About Sealed Air
Sealed Air is a leading global provider and manufacturer of a wide range of packaging and performance-based materials and equipment systems that serve food, medical, and an array of industrial and consumer applications. For more than half a century, Sealed Air employees around the globe have applied deep understanding of customers’ businesses to deliver innovative packaging solutions. Operating in 51 countries, Sealed Air’s widely recognized and respected brands include Bubble Wrap® cushioning, Cryovac® food packaging technologies, Jiffy® protective mailers and Instapak® foam-in-place systems. For more information about Sealed Air, please visit the Company’s web site at http://www.sealedair.com/.
The pulse of the packaging community